Latest News

At the latest meeting of Priority One’s Circular Construction Collective, construction leaders, builders, innovators and environmental experts gathered to explore one of the built environment’s most stubborn challenges: plastic. The group heard from two innovative businesses that have circular solutions to the problem material: Cleva Pod and saveBOARD.
saveBOARD: Turning plastics waste into building materials
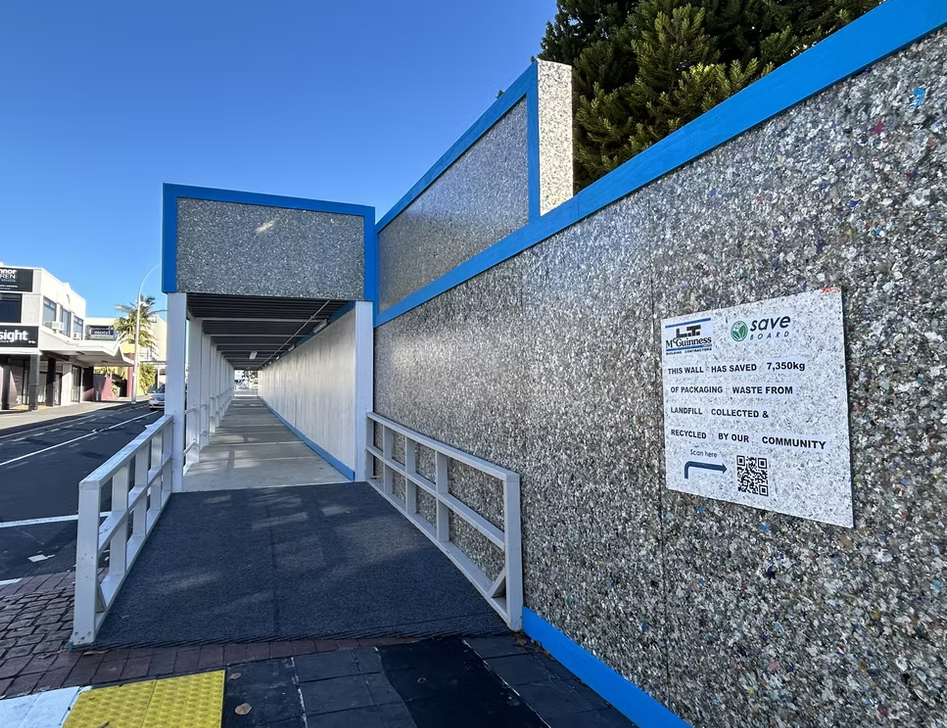
If you’ve strolled past the Te Manawataki o Te Papa construction site in Tauranga, you might’ve noticed the hoardings wrapping around the LT McGuiness site (pictured above). Not only do they look pretty cool, but they are a sustainability statement courtesy of saveBOARD – every 100m of its hoarding panels diverts around 3,000kg of packaging waste from landfill.
saveBOARD is a company turning plastic waste into high-performing building materials. Its products are made entirely from materials: soft plastics, food and beverage cartons (eg alternative milks, juices), and even construction site waste like timber wrap, shrink wrap, bubble wrap and plastic backing sheets. This waste is processed and repurposed as durable, mould- and moisture-resistant boards, designed to replace traditional materials, such as plasterboard and plywood.
The company has developed a range of low-carbon building products, from exterior bracing panels, interior wall linings and ceiling tiles to roofing substrates and joinery panels – all made with zero water, no glues and no harmful chemicals.
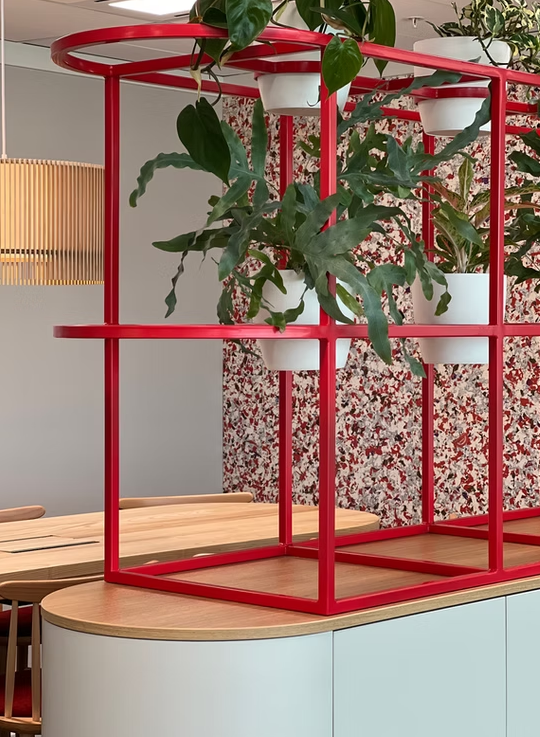
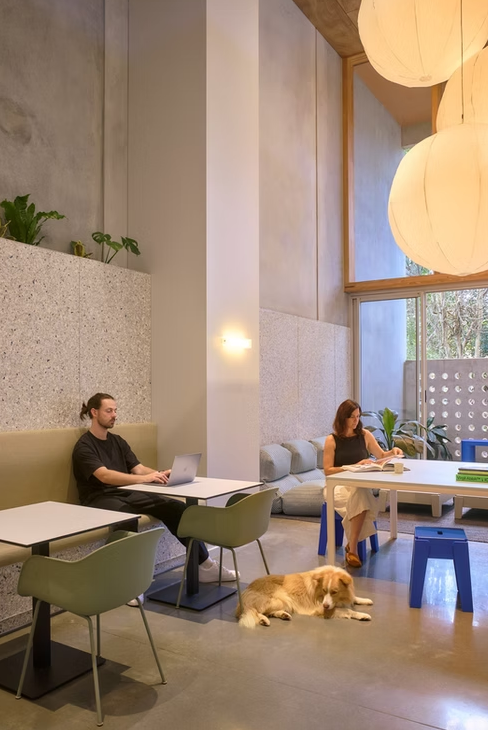
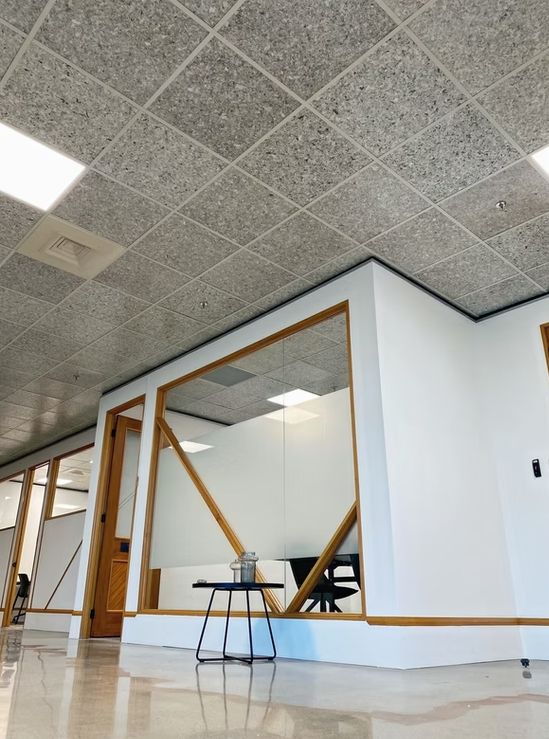
Raising awareness
Major clients are on board already: Woolworths and BNZ have used its interior wall linings, while Gartshore has integrated boards into national iSite refurbishments. Elevate Homes, a residential builder, is incorporating its rigid air barrier product (used to close-in builds from the weather), and construction group Livingstone is also using the hoardings on commercial projects. Check out the gallery of finished products.
While it may seem new to many, the technology behind saveBOARD has actually been used for over 20 years in the US and even longer in Europe. The New Zealand plant, located in the Waikato, currently produces around nine tonnes of product each week, with the capacity to scale up to 30 tonnes. The challenge now is awareness: getting architects, specifiers and everyday builders on board so this more sustainable alternative becomes a mainstream material.
Product stewardship
A standout aspect of saveBOARD’s model is its commitment to product stewardship. Construction offcuts and clean waste boards can be separated during the build process and returned to saveBOARD for reuse – a rare example of a closed-loop system in the building sector.
For locals, Tauranga’s Te Maunga Transfer Station serves as a drop-off point for plastic waste items, where they are collected and sent to saveBOARD for processing.
More than just upcycling, this is the circular economy model in action, with a zero-waste philosophy at its core.
Cleva Pod: Laying the groundwork for a more sustainable build
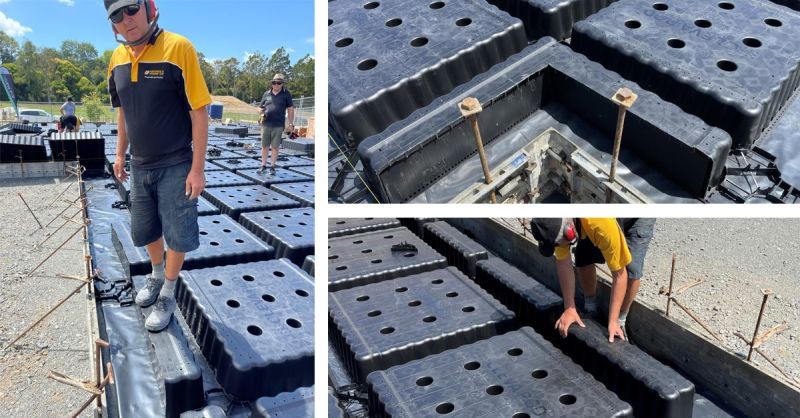
Cleva Pod is redefining how we think about building foundations with a sustainable, circular approach.
Traditional concrete foundations, use void-forming pods made from polystyrene to reduce the volume of concrete. However, polystyrene is a notorious environmental offender. Non-biodegradable, and nearly impossible to recycle once encased in concrete, and prone to breaking into small weightless beads that often end up polluting waterways and filling landfills.
Cleva Pod offers a better alternative: pods made from 100% recycled and waste plastic. These function just like their polystyrene counterparts but they’re part of a closed-loop system. Unlike polystyrene pods, Cleva Pods can be recovered and recycled , even after being used in a concrete slab.
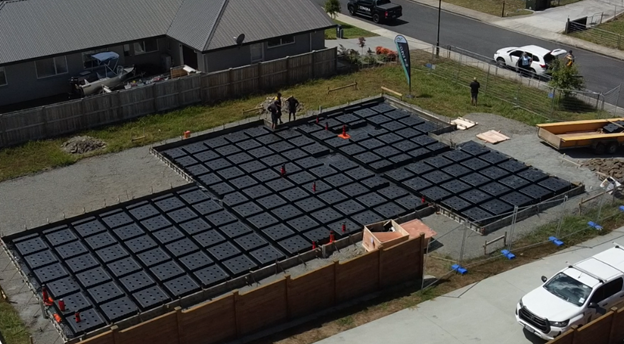
Cleva Pod’s design is practical and versatile. They can be cut to fit any slab configuration, whether for residential, commercial, or industrial buildings. They also stack efficiently — enough to supply the foundations for 10-12 average-sized homes can fit in a single 40-foot shipping container.
Installation is clean and straightforward. For builders, there’s no need for special training or tools, and the process is similar to existing construction practices, minus the mess and waste.
Perhaps most impressively, Cleva Pods make circular construction a reality. At the end of a building’s life, the concrete, steel and plastic can be separated and recycled — a big step forward for sustainable construction (see video above).
Learn more about Priority One’s Circular Construction Collective and the inroads it’s making into industry waste challenges.
To hear more about the latest in sustainable products, checkout this upcoming event: Sustainable Solutions – Leading the Way